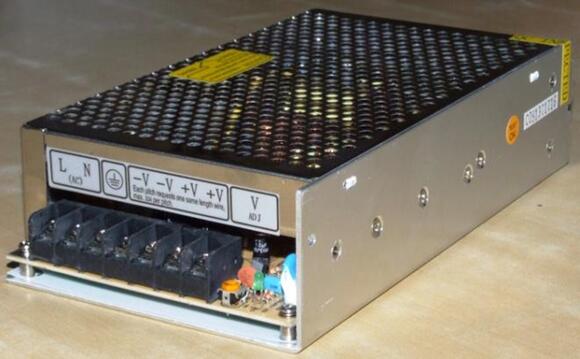
In industrial applications, the application of non-contact sensors is slowly becoming mandatory. These include proximity and photoelectric sensors which are used in sensing the presence, distance and even movement of objects without touching them. To the B2B firms operating in the industrial automation industry, it is crucial to grasp the different uses of the non-touch sensors to enhance the effectiveness, safety, and productivity of the operations. These sensors are crucial for industrial automation companies to develop smooth, efficient systems which can support today’s production requirements.
This article aims at explaining the different uses of non-touch sensors in industries, and how they enhance productivity in organizations.
Enhancing Equipment Safety
Non-touch sensors are very essential in enhancing safety of the equipment in industrial settings. Since these sensors do not require a direct touch with the object they are measuring, they are well suited for measuring dangerous or sensitive equipment. For example, proximity sensors are used to avoid accidents that may be caused by a human or an object getting too close to the restricted area by shutting down the machine. This is especially so in industries such as manufacturing and automotive where heavy equipment is used and is always running.
Photoelectric sensors are also useful in preventing production lines from running in a dangerous manner. These sensors work on the principle of light emission and reflection making them suitable for use in areas with moving parts. Non contact sensors eliminate wear and tear of equipment hence reducing the frequency of maintenance and therefore cutting on downtime expenses. For industrial automation companies, it means operations that are safer and more reliable in their execution.
Improving Product Quality Control
Quality assurance of the products manufactured is one of the most common uses of non-touch sensors in industries. Non-contact sensors make sure that production lines run smoothly and this can make manufacturers identify defects and other issues with the materials that they are working on. Proximity sensors can be used to determine the distance between two objects or to check that during assembly the parts are in the correct position and that every manufactured product is of the required quality.
Photoelectric sensors are best used for the sensing of small objects especially in the food industry where detection of small objects is very important for quality control. In automated systems, these sensors help in continuous monitoring and control in a way that minimizes the production of substandard products that may end up with the customers.
For instance, a switching-mode power supply (SMPS) manufacturer can incorporate non-touch sensors during the assembly process to identify misalignments or incomplete parts and guarantee that every unit produced is efficient and safe before it is sold.
Streamlining Automated Processes
It is therefore important to incorporate Non-touch sensors to enable easy automation of processes in industries. Through the use of proximity and photoelectric sensors in automation systems, manufacturers are able to have their machines run for long hours without being monitored by human personnel. These sensors identify the existence or non-existence of objects and elicit appropriate responses from the machines to allow smooth, autonomous running.
For instance, in automated packaging systems, photoelectric sensors are used to determine when the products are ready for packaging, thus, the packaging machine only runs when required. This not only increases the speed of production but also decreases the consumption of energy and use of materials. This comes as a boost to industrial automation companies since they are able to produce more as they reduce the costs of operation.
Also, the proximity sensors are commonly applied in conveyors to identify items and guide them to the appropriate positions. This minimizes chances of making mistakes while sorting the items and it helps in ensuring that the items are processed in the right order thus making the automated process more efficient.
Reducing Equipment Wear and Tear
Contact-based sensors on the other hand are detrimental to both the sensor and the equipment since they wear out the equipment as well as the sensor. This can lead to early replacements, expensive maintenance and product down time. Non-contact sensors, in contrast, decrease mechanical stress, which results in the longer service life of equipment.
In industries where the machines are fast or handle delicate items then the non-touch sensors such as the proximity and the photoelectric sensors have a big advantage. They observe the conditions of machinery and production processes without creating wear and tear or mechanical pressure which are essential in extending the life of machines in industries.
For instance, a proximity sensor applied in a CNC machine can identify the position of tools without making contact with them and therefore minimize the wear of the tool as well as the sensor. This results in less need for maintenance and more operating time, which is advantageous for an SMPS manufacturer as it means that the manufacturer’s product will have less defects and more durability.
Optimizing Inventory and Resource Management
Non-touch sensors can also help to improve the control of inventory and resources in industrial settings. For example, proximity sensors can help manufacturers know when the stocks of materials or components are getting low so that they can order for more before they exhaust their stock. This reduces the chances of being faced with material shortages which may lead to disruption of operations and hence, the production process is continuous.
Photoelectric sensors can also be used in warehouse automation, for example, when items are stored in bins or on conveyors. This makes it possible for the warehouse management systems to be able to track the inventory in real time and thus avoid situations where there is over stocking or under stocking of the commodities.
The use of non-touch sensors in inventory management systems will make industrial automation companies optimize on their resources hence save on costs and make their operations more sustainable.
Non-touch sensors are revolutionizing industrial settings by increasing safety, quality control of products, efficiency of automation, and decreasing equipment deterioration. These technologies include proximity sensors that detect objects without any physical contact, photoelectric sensors that monitor high-speed parts, among others, are very important for efficiency and production.
Thus, the use of non-touch sensors in systems of industrial automation companies helps them meet the new demand for increased accuracy and safety in the modern industry. Likewise, an SMPS manufacturer can better the quality of the product, cut the maintenance cost and increase the efficiency of the production process through the use of non-touch sensors.
Non-touch sensors will continue to be a key component of industrial systems as the automation progresses, which will lead to more efficient processes and improved results of companies in different fields.
Comments / 0