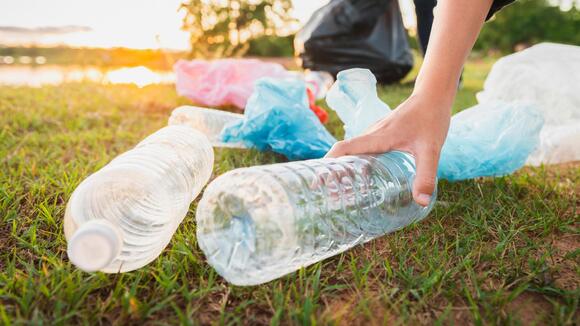
Researchers at the University of California, Berkeley, have unveiled a chemical process that has the potential to revolutionize plastic recycling.
This innovative process can effectively vaporize the most common types of plastic waste. Subsequently, it turns common plastic waste into useful materials for making new plastics.
John Hartwig, a UC Berkeley professor of chemistry who led the research, explained this new development and its benefits while talking to Interesting Engineering.
The catalytic process can effectively break down polyethylene and polypropylene, which together constitute a staggering two-thirds of all post-consumer plastic waste globally.
“We have an enormous amount of polyethylene and polypropylene in everyday objects, from lunch bags to laundry soap bottles to milk jugs — so much of what’s around us is made of these polyolefins,” said Professor Hartwig in a press release .
This new process converts them into valuable hydrocarbon building blocks suitable for reuse in the production of new plastics. It could lead to a circular economy for many throwaway plastics, significantly reducing the need for new plastics derived from fossil fuels and mitigating the environmental impact of plastic waste.
Overcoming limitations
This development builds on previous research by Hartwig and his team, which focused on breaking down polyethylene into propylene.
The researchers highlighted a key advantage of the new tungsten oxide and sodium on alumina catalysts over the precious metal catalysts used in their prior work.
“The prior catalysts were active, but not long lived and could not be regenerated and reused. In addition, the prior catalysts did not work on polypropylene,” Professor Hartwig explained to IE.
“The new ones will deconstruct polypropylene and react with higher turnover numbers (moles of product/mol of catalyst; a measure of lifetime) and can be used through multiple reaction cycles.”
The new catalysts eliminate the need to remove hydrogen to create breakable carbon-carbon double bonds in the polymer, a crucial step in the previous process.
They are also highly efficient, converting a nearly equal mixture of polyethylene and polypropylene into propylene and isobutylene with nearly 90% efficiency.
Impact of plastic additives
The researchers also found that the process is resilient to some plastic additives, as demonstrated by successfully deconstructing various everyday plastic objects.
However, their research indicated that certain additives, such as poly(vinyl chloride) (PVC) and polyethylene terephthalate (PET), can poison the catalyst, hindering its effectiveness.
Fortunately, these materials can be readily separated from polyethylene and polypropylene.
“Our catalyst was tolerant of polystyrene, which would be a contaminant more difficult to separate by density,” Hartwig told IE.
“The catalyst was also poisoned by phthalate additives. There are many other additives and impurities that can be present in waste plastics, and future work will be conducted to test the tolerance for them.”
Scaling up for industrial applications
The shift to solid catalysts has paved the way for a continuous flow process, a method widely employed in large-scale industrial reactions due to its efficiency and scalability.
“Most large-scale industrial reactions are conducted as a continuous process. It is just too cumbersome to run batch after batch to create tons of products.”
The new approach presents several key advantages. Firstly, it facilitates easier catalyst recovery and reuse, leading to cost savings and reduced environmental impact.
Secondly, continuous flow processes offer enhanced control over reaction conditions, enabling better management of product quality and yield.
Future research and development
The researchers have identified key areas for further development and optimization of the process.
They are actively working on improving catalyst lifetime and regeneration, particularly for the sodium on alumina catalyst.
“We also need to work on configurations of the reactor to scale up and learn more about the effect of additives and impurities,” Professor Hartwig concluded.
While challenges remain, including the impact of certain plastic additives and the need for further scaling up, this breakthrough represents a significant step toward a more sustainable future for plastic waste management.
Comments / 0