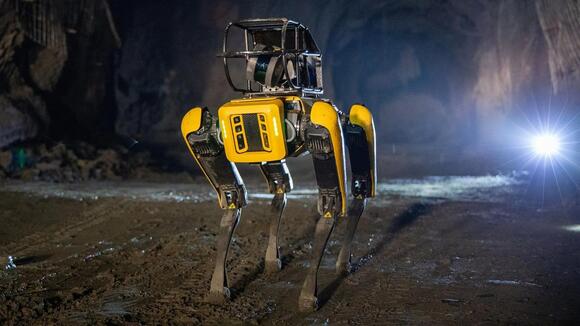
A robot that can help prevent the growth of weeds on farms without the use of harmful herbicides has been created by researchers.
Texas A&M University’s team has come up with an effective weed control system and algorithm for a Boston Dynamics Spot quadruped.
The robot uses a flexible end effector to handle changes in the environment, such as gravity, wind, atmospheric pressure, fuel tank pressure, and nozzle position, which can affect the flame’s coverage.
According to the team, experiments showed that the system works, and its model and algorithm can achieve over 76 percent accuracy in predicting reprojected images in real time.
Robotic weed control
Weed infestation is a persistent issue in agriculture, as weeds compete with crops for nutrients, water, and sunlight. Manual removal is labor-intensive, and mechanized herbicide spraying harms the environment. Robotic weed removal offers a new solution.
Researchers aimed to develop eco-friendly methods to control weeds in their early growth stages. They report progress on a robotic weed-flaming solution using a mobile manipulator equipped with a propane torch. Instead of burning weeds, the robot targets and heats the plant’s center, effectively stunting its growth for several weeks.
“To enable precise weed removal, the greatest challenge is to detect and predict dynamic flame coverage in real-time before motion planning, which is quite different from a conventional rigid gripper in grasping or a spray gun in painting,” said the researchers in the study.
The team’s system uses Boston Dynamics ‘ Spot Mini quadruped robot with a Unitree Z1 manipulator arm. The arm can carry up to 3.2 pounds (2 kilograms) and is powered by Spot’s internal battery.
According to the team, the system is enabled by a DC-DC converter that powers the arm and onboard computer. An Intel Realsense D435 RGB-D camera detects weeds, while two FLIR Lepton 3.5 thermal cameras monitor the flame.
The onboard computer handles perception, decision-making, and control. A propane tank supplies gas to the torch, which is ignited by a relay-controlled lighter. Hand-eye calibration ensures accurate alignment of the cameras, manipulator, and end-effector for effective weed flaming.
On the software front, the system uses a YOLOv6 model, which is a single-stage object detection framework for industrial applications, to locate the weed roughly. The Spot robot then plans a path to get close to the weed using its software kit.
Once in position, the RGB-D camera detects the weed’s center, and the system estimates the flame’s surface for accurate flaming. Finally, the robot’s arm position is planned using the Unitree arm software for effective weed removal.
Advanced weed flaming
To test the online flame estimation algorithm, researchers collected 156 pairs of images using thermal cameras in a controlled indoor environment. They classified the images based on light or strong wind conditions.
The team used the data to estimate a circular arc flame model and compared it to a baseline straight-line model. The circular arc model performed better in both light and strong wind conditions.
While both models gave similar results in light wind, the straight line model’s performance declined in strong wind, unlike the circular arc model.
Additionally, the team conducted experiments on a raised bed plot and a cotton field to test their flaming system against various weeds.
The raised bed plot experiment involved five trials with random initial robot positions. The robot successfully detected, planned, and executed the flaming action on common weeds like sunflower, ragweed, and smell melon.
According to researchers, thermal images confirmed flaming coverage and showed 94.4 percent precision in targeting weeds. The cotton field experiment aimed to test the system’s performance in a real agricultural setting, and the results are shown in a multimedia attachment.
In the future, researchers will plan the motion of the mobile manipulator to achieve dynamic flame coverage for multiple weeds. They also aim to integrate new weed removal techniques, such as electrocution, into the robot.
Additionally, new algorithms will be developed to enhance the system and improve its efficiency. The team’s research was published in the journal arXiv.
Comments / 0