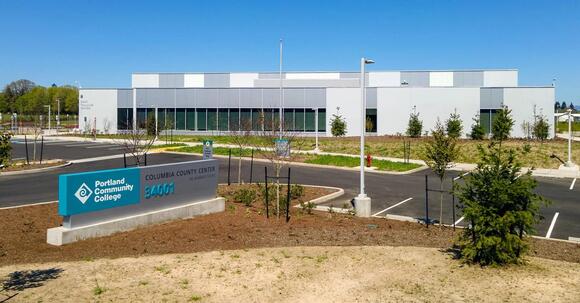
Columbia County, just north of Portland, has been at heart of the region’s manufacturing since the 19th century.
Here they made cobblestones for Portland’s first city streets and U.S. Navy ships for the first world war. Now Columbia County is making a new future with a rising new workforce, trading yesteryear’s timber milling for advanced manufacturing with new metal alloys and computer-aided design.
“Students are deciding as early as 4th grade, especially girls, if they will go into college or pursue a career in STEM or manufacturing. Outreach to younger students is vital,” said Sarah Burns, standing in front of a collection of 3D printed objects her students created. Burns is the coordinator of Portland Community College’s Fab Lab, teacher of all things maker, and coach of a Monday night community Lego robotics team. “This is the only place you can do welding, 3D printing and robotics — all at once.”
In a county where the average age (43) skews slightly older than state and national average (40), Portland Community College opened Oregon’s newest workforce training center in 2021.
The center has become a point of community pride, helping teens from rural towns of Scappoose and St. Helens (where most working people commute 20 minutes into Portland or Washington County) envision their own careers closer to home. And helping ensure regional employers have the workforce they need for tomorrow’s products.
“We ask industry: ‘What are we missing? What do we need?’ And then we do that,” said Patty Hawkins, director of the 25,000 square foot training center. “It’s a huge opportunity for companies. They have a steady stream of trained workforce.”
For some companies, PCC will even tailor a full curriculum custom-designed for individual company processes and the types of products they are making.
For all the national efforts to expand and re-shore US manufacturing, some have questioned whether today’s students even want jobs in that sector. In two years since opening its doors in Scappoose, PCC-Oregon Manufacturing Innovation Center (OMIC) Training Center has seen a clear answer.
“Come check out how full our classes are, it speaks for itself,” Hawkins said.
PCC-OMIC began offering in 2021 its low- or no-cost advanced manufacturing certificate to a cohort of four students. Today, the cohort is full with 24 students every semester, and the college is planning more to meet demand. Some students are in their first years of college. Others are mid-career.
In one spot, a student can train on precision measurement tools key to manufacturing and aviation sectors and a few steps away program a robot to pull items off a conveyer belt with PLCs (Programmable Logic Controllers).
“It’s useful to anybody. It’s logic and AI. The applicability is so wide,” Hawkins said.
As the center director Hawkins makes it her business to ensure career applicability is at the core of the student experience. She’s constantly on the lookout for matching the PCC training to the industry need in the region, and even moved her residence to Columbia County to more deeply work with the local community.
Paul Vogel, executive director of the Columbia Economic Team, has seen the impact of the PCC center from day one.
“There is an assimilation that had to happen. It’s not a campus; it’s a training center. This is a hub for the community, and it’s tied organically to OMIC R&D across the street.” he said.
At the Oregon Manufacturing Innovation Center, Research and Development (OMIC R&D), a 60,000-square foot two-building complex houses some of the world’s most advanced steel cutting, milling, and additive manufacturing machines. The facility plans to be one of the first in the U.S. to include all seven ASTM International recognized forms of additive manufacturing.
The regional focus, linking workforce development and manufacturing innovation and business incubation, is emblematic of Oregon collaboration. And the region’s top global manufacturers are all involved in it.
“We are really lucky to have the next step right here. We look to business, industry, OMIC R&D. They inform where we focus,” Hawkins said.
And in turn, businesses look to each other. Companies from Sweden, Germany, Austria, Japan, Korea, ranging from knife-makers to aerospace, all make major investments alongside state and federal grants to ensure they have access to OMIC R&D’s world class facility and research.
“All these companies have to know how to cut and shape metal,” said OMIC R&D founding executive director Craig Campbell. “We are like their backyard R&D shop.” This month Campbell was promoted to be special assistant to the president of Oregon Institute of Technology, the host university and owner of the OMIC R&D facility.
Formed in 2017, the collaboration among 37 industry partners, including regional leaders Daimler, Boeing, and Oregon Tool, can call on OMIC researchers and each other to problem solve about new manufacturing challenges.
“They may not mix outside in the economy, but they collaborate in here,” said Campbell of the members, who together represent 12,000 employees.
Global manufacturing leaders join OMIC (some paying over $300,000 annually) for three key reasons: access to world class R&D and to sell into Portland area companies, namely Daimler and Boeing, and to drive forward industry collaboration.
“There are not that many cutting tool manufacturers in the world, and almost all of them are members of OMIC R&D and are interested in having an impact here in the Pacific Northwest,” Campbell said.
At OMIC, companies can test-drive cutting edge equipment (pun intended), see how efficiently it can work, and realize the time and raw materials they can save by using these new tools and processes.
OMIC is unique in the range of manufacturing technologies it has at its fingertips. OMIC R&D is demonstrating how collaborative robots, or co-bots, can improve worker safety by working side by side with a human to lift 40 pounds of steel to place it in cutting machines and prevent back injuries.
With all these tools, OMIC R&D conducts projects that allow manufacturers to make their products better, faster, greener, and at lower cost. Essentially, OMIC is a working showroom of some of the best cutting machines and metal 3D printers in the world and a test bed to prove out what manufacturers need to overcome their next challenge, grow and thrive.
Much of OMIC R&D’s work is proprietary, but the lessons learned are shared with those who can use it to improve. Materials from their Scappoose site head across the river to become part of Daimler trucks or fly around the world as part of F-15 jets.
Companies looking to make their own metal alloys can also access the first of its kind blast proof room at OMIC’s Additive Manufacturing Center, opened in 2023, to mix elements and test new products.
Given the high-end nature of the equipment on site — think 6,000 pounds of steel being able to turn on five different axes and then cut to be one piece strong enough to power a jet engine — OMIC provides training to ensure a company’s workforce can use these new tools.
OMIC R&D also provides a virtual reality training for high school students to learn how to operate the leading-edge machines. The VR program that was given to area schools through a grant from Congress.
Oregonians know a thing or two about saws from generations of wood mills. The last mill in St. Helens, Cascades Tissue, closed in October 2023. But the skill involved and attention to detail and safety are more transferrable than one might think. A steel beam and a log present similar challenges to lift, twist and turn toward a blade.
At a time when employers worldwide are hungry for industrial land and talent, Greater Portland offers both.
“The difference is, we in Columbia County have the space,” said Vogel. OMIC R&D itself is surrounded by 400 acres of shovel-ready industrial land.
Columbia County has an industrial building vacancy rate of 17.2%, according to commercial real estate database CoStar. That’s triple the availability of the seven-county Greater Portland region (4.7%) through March 2024.
“This area is perfect for manufacturing, especially for those companies where access to — but not sitting right alongside — Interstate 5 is less important,” said Vogel.
And since COVID, Columbia County’s rural lifestyle has also been a draw for talent with its livable community, river access and quieter pace.
PCC OMIC and OMIC R&D have breathed new life into the region benefiting the community itself as much as the companies depending on the talent pool.
Matt Presley considers himself a “lifer in the trades.” He owned a cabinet shop for years, but when the PCC OMIC training center came in, he shifted to computer-aided design to templatize his projects, and now he’s teaching that skill to a new workforce.
“This place was built in my backyard,” he said of the training center. Then, looking out the windows over space where PCC OMIC has room to double the training center’s size, and seeing the students working on machines next to him, he smiled. “You can really envision the future.”
Comments / 0